Applications
Grinding and ECG Cutoff Machine Applications Library
Glebar machines are used in the medical industry to produce medical devices where high precision is needed.
Our versatile precision grinding machines are workhorses that require a smaller footprint than similar machines yet excel in demanding high-production environments where the name of the game is high volume at low cost. Glebar engineers can tailor a medical precision grinding turnkey solution, complete with a series of pre-and post-grind inspection steps, ensuring the product going into the Glebar machine meets the requirements of the final ground product with guaranteed accuracy.
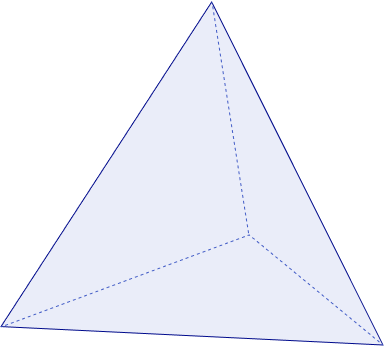