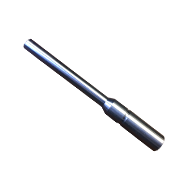
Challenge: A food equipment manufacturer approached Glebar to improve productivity and reduce costs for their food filler machines. The metal spout requires grinding for several reasons. They come in contact with food, therefore requiring a smooth finish for sanitary purposes. The tubes are often exchanged on the machines to dispense various size pastries. Also, the mating housing for the spouts must be a close fit to prevent leaking and to keep appropriate content pressure to dispense the precise amounts. Eight different components needed to be ground, all approximately four-inches in length, however they varied in diameters and weight. The variation of part geometries posed the biggest feeding challenge. Rapid changeover of grinding wheels was important to reduce setup time between the components.
Solution
The automated GT-610 Centerless Grinding system was selected to address the various part geometries. The system was equipped with a large 30” bowl feeder to accommodate the long tubes. Centerless grinding the tube provides a better surface finish versus a screw machine or other competing methods. Running eight different parts throughout the system was done through the use of an adjustable work rest blade – easily adjustable via our unique ramp device allowing the user to adjust the height by simply turning a screw, making setup easier. Competing methods must rely on shimming the wheel which is less accurate, slower and does not provide the same roundness.
The 8 5/8” width of the GT-610’s grinding wheel was ideal for the parts’ geometry, allowing for spreading the material removal over longer distances providing a more efficient grind. To automatically feed this part, the spouts were orientated to go in major diameter first. If not fed in this manner an imbalance would occur, resulting in parts toppling over each other.
A variable vibratory driver, connected to the feeder plate components, controls the speed at which the parts travel. The parts then index up as a single layer to the feeder discharge where they are subsequently transferred onto a conveyor vibratory inline system taking them through the grinding wheel. The material removal requirements were met with a cycle time of approximately 10 parts per minute while holding a .0004” diameter tolerance.
The material removal requirements were met with a cycle time of approximately 10 parts per minute while holding a .0004” diameter tolerance.
Running eight different parts throughout the system was done through the use of an adjustable work rest blade – easily adjustable via our unique ramp device allowing the user to adjust the height by simply turning a screw, making setup easier.

Explore | GT-610 Infeed/Thrufeed Centerless Grinding Machines
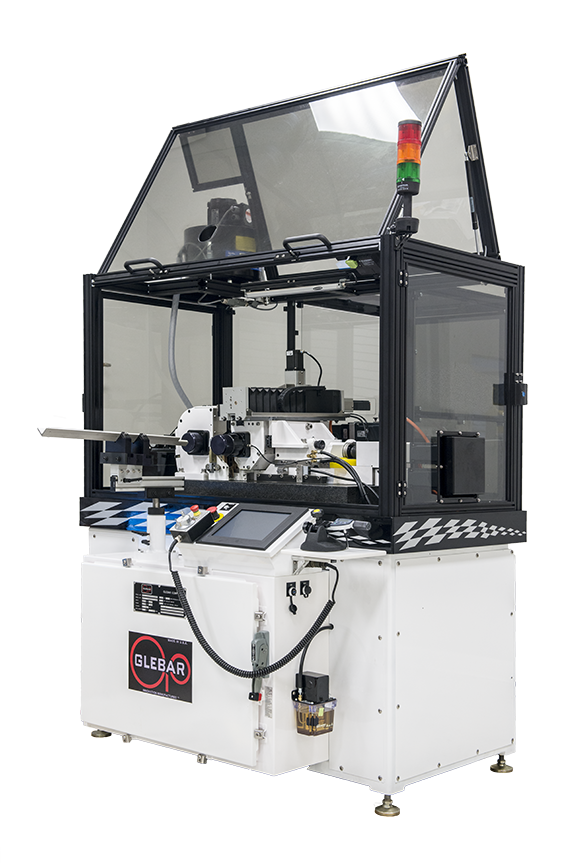
GT-610
The GT-610 Automated Infeed/Thrufeed Centerless Grinding Machine can be custom fitted with automation. This system is the ideal option for when infeed applications do not require a CNC dresser and for the vast majority of thrufeed applications. The GT-610 excels at hard metals and composites, producing carbide blanks, spools, bushings, and engine components such as automotive fasteners and valve lifters. It can also effectively size down metal bars.