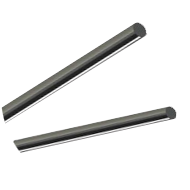
Current Process:
The grinding of stainless-steel shafts used for Hydraulic Spring Lifters was outsourced. This resulted in higher costs, as well as quality and consistency issues.
Challenges:
Deliver an in-house process to automatically grind a high volume of stainless-steel shafts used for Hydraulic Spring Lifters. The process had to remove a large amount of stock and maintain an 8Ra surface finish. The customer requested that the new process be integrated with their existing automation and superfinishing line.
Solution
Solution: GT-610 Thrufeed Centerless Grinder featuring Lights-Out Automation
This GT-610 Thrufeed Centerless Grinder is equipped with a conveyor, pre-feed and post-feed sensors, contact gauge, and complete safety enclosure. HMI controls allow one-touch start/stop operation and the use of inline gauging. As the stainless-steel shafts travel down the conveyor, they pass through the pre-feed sensor which initiates automatic feeding into the grinder. The shafts are fed through the grinding area removing .021″ of stock material in one pass. A diameter tolerance of +/- .00020″ and roundess in the 50 millionths range was maintained.
The contact gauge inspected the parts for geometric accuracy and defects. The measurement data from the in-line contact gauge can be sent back to the GT-610 for automatic adjustment to compensate for any wheel wear, improving grind accuracy.
The post-feed sensor counts the parts for automatic dressing which improves consistency.
Glebar worked with two other companies to integrate the GT-610 into the customer’s existing automation and superfinishing line.

Explore | GT-610 Infeed/Thrufeed Centerless Grinding Machines
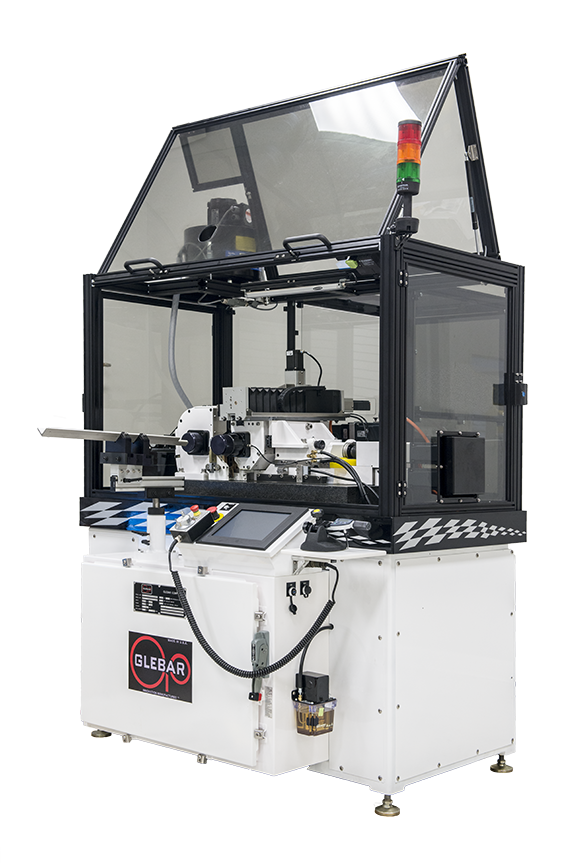
GT-610
The GT-610 Automated Infeed/Thrufeed Centerless Grinding Machine can be custom fitted with automation. This system is the ideal option for when infeed applications do not require a CNC dresser and for the vast majority of thrufeed applications. The GT-610 excels at hard metals and composites, producing carbide blanks, spools, bushings, and engine components such as automotive fasteners and valve lifters. It can also effectively size down metal bars.