Current Process
Hydraulic dress cycles require high operator input reducing their efficiency. The traverse rate of the dressing tool is difficult to establish affecting surface quality. Inconsistent dressing of the work wheel reduces machine efficiency and can lead to higher scrap rates.
Challenges
Develop a process to dress the regulating and work wheel that improves operator and machine efficiencies, improves control of the traverse rate, maintains a high-quality part, and reduces scrap rates.
Solution
Solution: Automatic Work Wheel Dressing. Available on all of Glebar’s TF-9DHD and GT-610 machines.
An operator can initiate the automatic dressing cycle from the HMI leaving them free to perform other tasks. The frequency of dress can be preprogrammed to automatically refresh grinding wheels after a set number of cycles or time, maintaining a consistent grind and a high-quality surface finish. Available with either manual quill advance or motor-driven quill advancement
Operators can control the traverse rate producing a more controllable and predictable wheel dress in both the regulating wheel and work wheel improving the surface quality of the part being ground.
Output increases by preprogramming the frequency of dress automatically after a set number of cycles or time.
Initiating the dressing cycle from the HMI improves operator safety eliminating the need to reach inside the work area making the machine much safer.
With motorized quill advancement it is possible to have a canned dress cycle; roughing and finishing the wheel unattended allowing one operator to run multiple machines.
Typical Glebar installations have one operator running 3 or more machines because of the reliability of the automation and grinder performance.

Explore | TF-9DHD Micro Grinding Machines
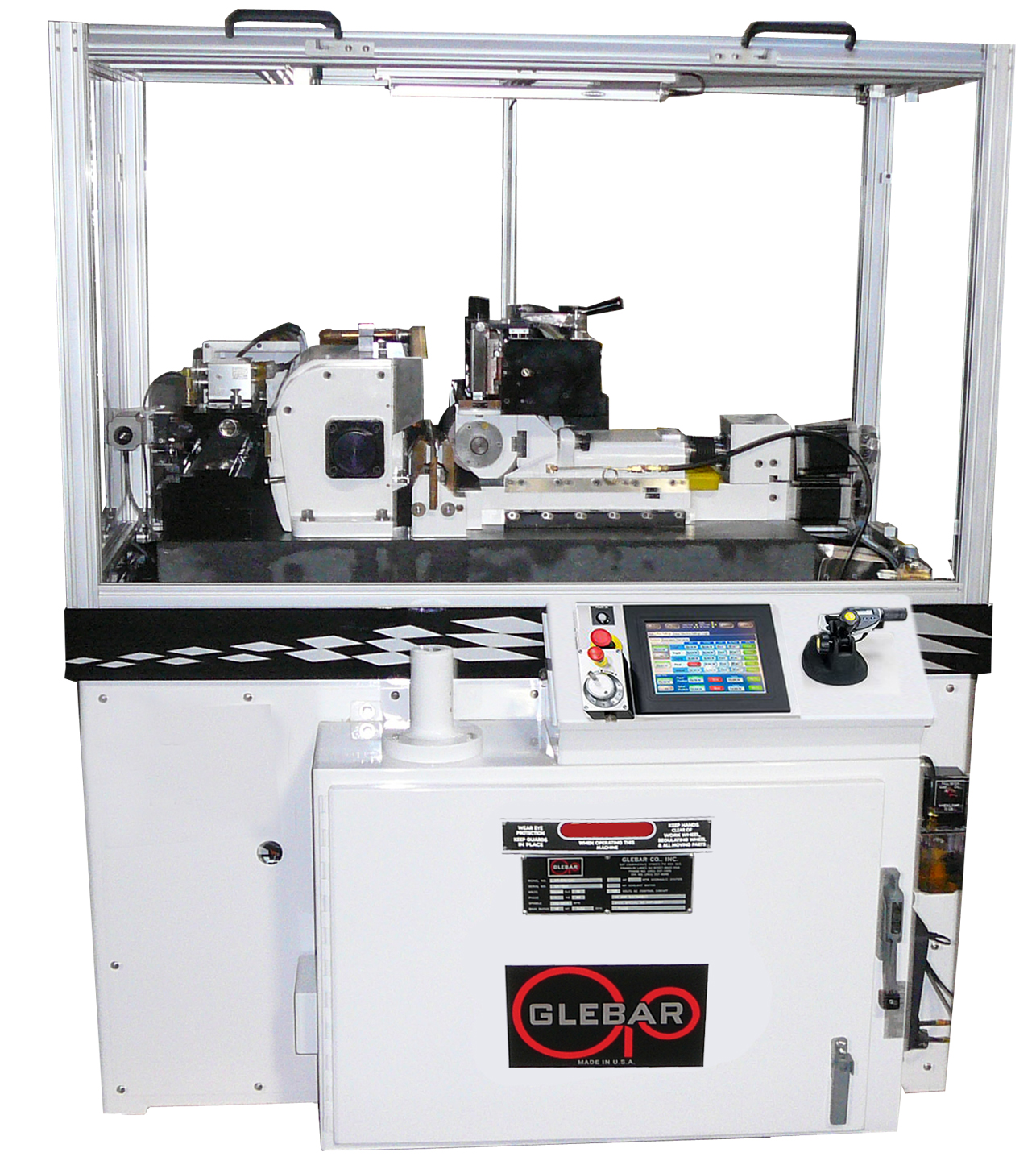
TF-9DHD
The computer controlled TF-9DHD Infeed/Thrufeed Micro Grinder grinds both hard and soft materials, specializing in parts from 1” in diameter down to .002″. The TF-9DHD is utilized to grind catheter, guidewires, pins, bushings, PTFE, plastics, ceramics and other engineered materials.