Challenge: To auto thrufeed grind metal valve seat components which are used in the automotive industry. The customer needed a system which could accurately grind and gauge 3,000 parts per hour. The width and nonsymmetrical geometry, would be the most difficult challenge engineers would face in devising a successful staging and feeding process as they are not able to line and stack up onto a traditional conveyor without falling over.
Solution
Glebar exceeded the customer’s challenge by grinding 5,000 parts per hour by designing and configuring a GT-610 Thrufeed Grinding System fitted with a hopper and vibratory bowl feeder which introduce the stream of parts into the machine. The unique part of the process comes next, when the components are strung onto a wire and then fed into the grinding area. The machine then centerless grinds the 0.4545” diameter parts to the required +/-0.0002” tolerance. At the exit side of the machine, another conveyor leads the parts through an air knife for cleaning then to a laser gauge for measurement and automatic size compensation. This Case Study was also the focus of a Feature Story in Today’s Motor Vehicles.
5,000 parts per hour (vs. 3,000 the customer requested)
0.4545” diameter parts ground to the required +/-0.0002” tolerance
Explore | GT-610 Infeed/Thrufeed Centerless Grinding Machines
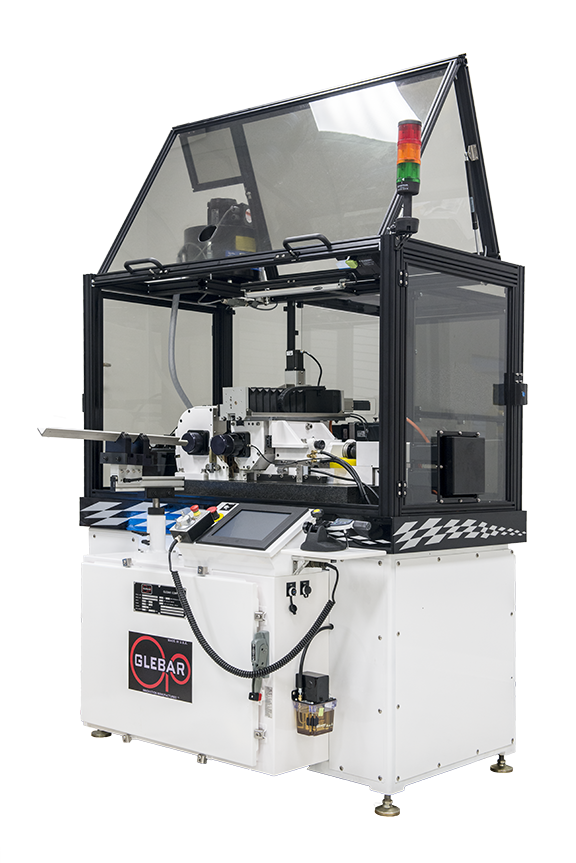
GT-610
The GT-610 Automated Infeed/Thrufeed Centerless Grinding Machine can be custom fitted with automation. This system is the ideal option for when infeed applications do not require a CNC dresser and for the vast majority of thrufeed applications. The GT-610 excels at hard metals and composites, producing carbide blanks, spools, bushings, and engine components such as automotive fasteners and valve lifters. It can also effectively size down metal bars.