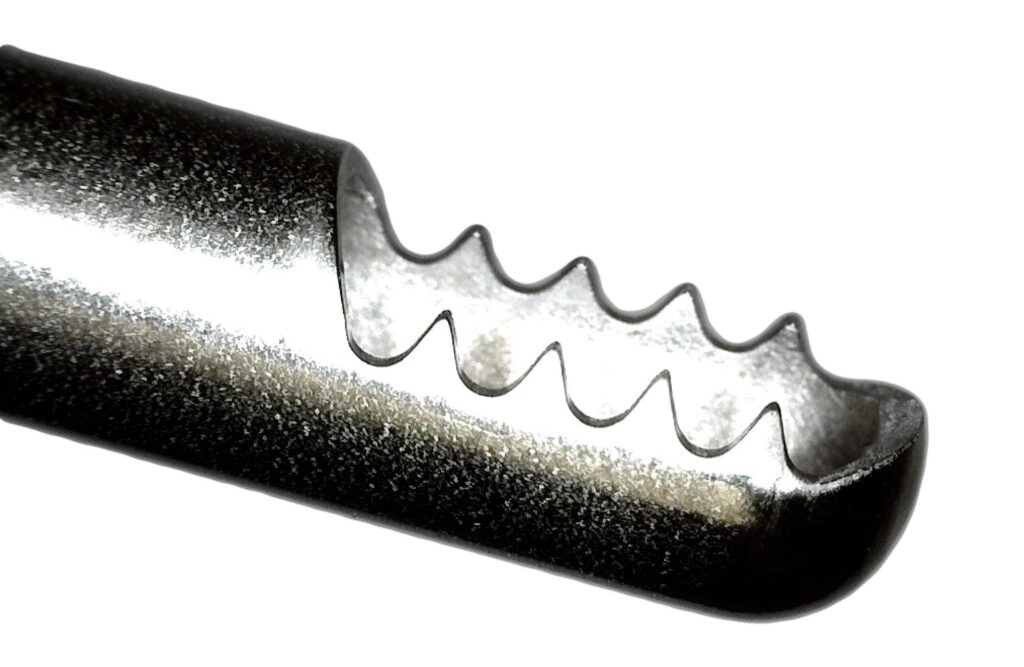
Challenge
The arthroscopic shaver teeth are commonly produced by conventional abrasive grinding, wire EDM, or laser cutting; slow processes resulting in long cycle times. EDM and laser cutting burn away the metal at high temperatures leaving changes to the metal surface including a heat affected zone, recast, and slag. Laser cutting requires significant post processing to produce an acceptable sharp edge and surface finish. Conventional grinding requires a secondary process of deburring without damaging the cutting edge. It also involves frequent wheel dressing to maintain the correct form.
Design a process that can cut shaver teeth burr free, without recast, slag, or heat damage that improves cycle times.
Solution
Solution: Glebar Burr Free Electrochemical Surface Grinders SG-1645 and SG-2060
Electrochemical grinding provides a burr-free grind for applications with tight tolerances and heat sensitivity. Curved shaver teeth are ground individually, whereas straight cut shaver teeth can be stacked up to 30 parts at a time with typical cycle times of 10 seconds per piece. Each machine features CNC controls and high precision components for high accuracy and repeatability. Optional pallet loader features a 180-degree index table allowing parts to be loaded during the grinding operation reducing loading time to almost zero, maximizing productivity.
Provides a burr-free cut in one pass with no heat affected zone, recast layer, or work hardening of the material.
The ECG technology can cut full depth in one pass requiring less wheel dressing with wheel life lasting up to 20x longer.
Electronic interlocks, safety rated servos and pneumatics are used to achieve CE and ISO 13849 Safety Certifications.
Explore | SG-2060 Burr Free ECG Surface Grinder
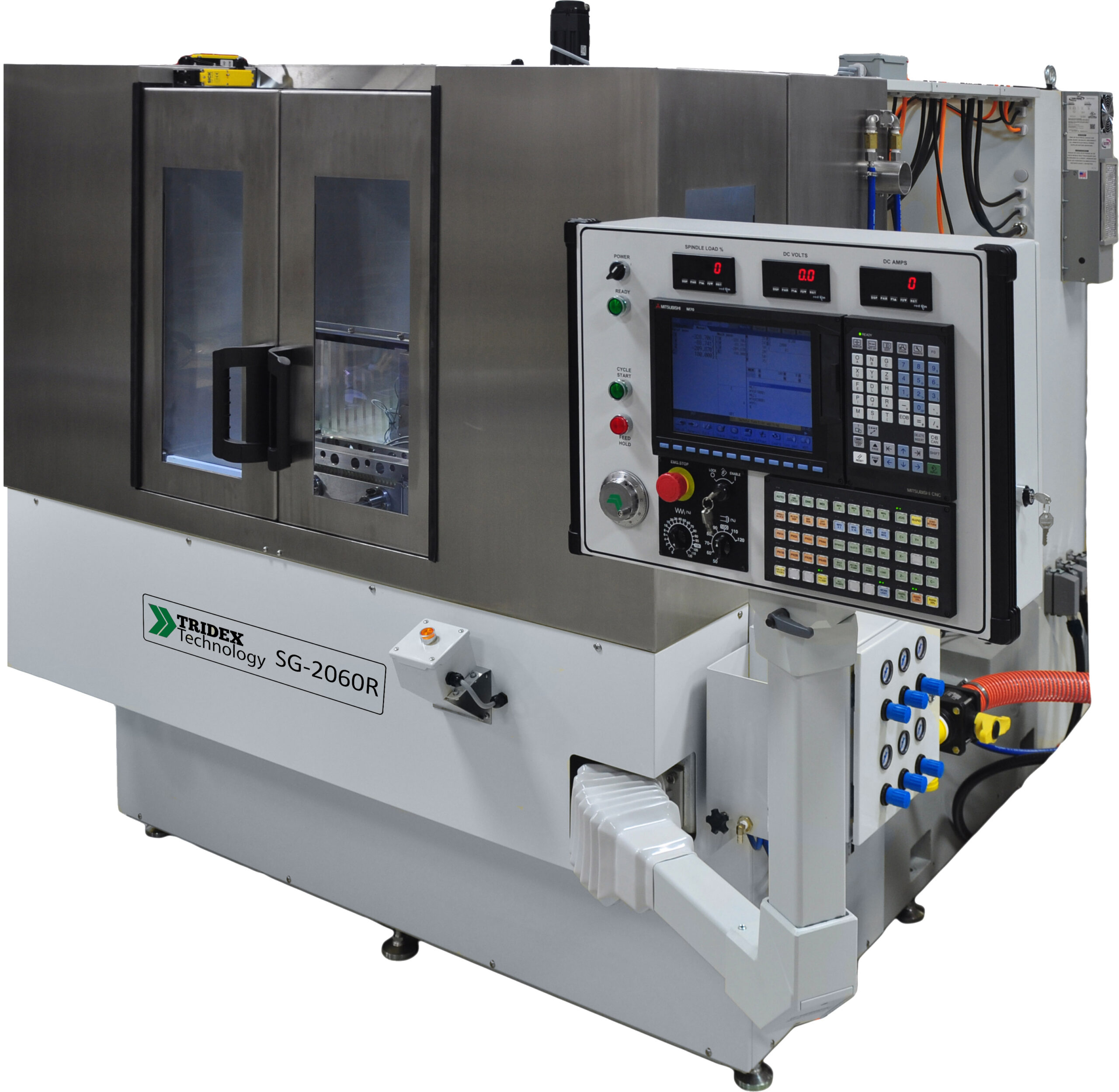
SG-2060
The SG-2060 Burr Free Electrochemical CNC Surface Grinder from Tridex Technology provides burr free and low force cutting leaving no heat affected zones while cutting. It has numerous applications across many materials and industries including medical device, automotive, and aerospace.