Automatic Work Wheel Dressing
Current Process
Hydraulic dress cycles require high operator input reducing their efficiency. The traverse rate of the dressing tool is difficult to establish affecting surface quality. Inconsistent dressing of the work wheel reduces machine efficiency and can lead to higher scrap rates.
Challenges
Develop a process to dress the regulating and work wheel that improves operator and machine efficiencies, improves control of the traverse rate, maintains a high-quality part, and reduces scrap rates.
Solution: Automatic Work Wheel Dressing. Available on all of Glebar’s TF-9DHD and GT-610 machines.
An operator can initiate the automatic dressing cycle from the HMI leaving them free to perform other tasks. The frequency of dress can be preprogrammed to automatically refresh grinding wheels after a set number of cycles or time, maintaining a consistent grind and a high-quality surface finish. Available with either manual quill advance or motor-driven quill advancement
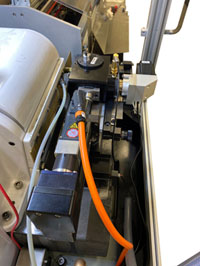
Upgradeable Machines
GT-610
Infeed/Thrufeed Centerless Grinding Machines
GT-9AC
Micro Grinding Machines
Traditional guidewire centerless grinders use sensors to detect the wire position and trigger diameter changes, limiting the number of tapers the system can produce. Since the GT-9AC has no sensors,…
TF-9DHD
Micro Grinding Machines
Simple to operate machine with the operator in mind. Reduced setups are a result of a thoughtful design of the machine. Independent top and bottom slide controls, simple work rest…